Metal powder forming hydraulic press
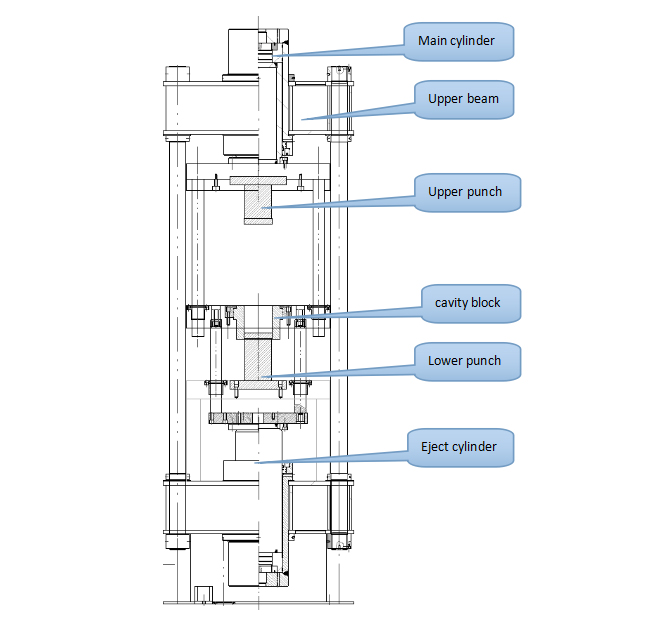
Mould Frame
1) The mold base is mainly made of 40Cr and 45# steel by forging, turning and fine grinding to ensure sufficient steel and matching precision. The guide surface adopts material differentiation to protect the surface from abrasion, such as copper guide sleeve. With Cr.
2) The upper mold part of the mold frame is a single upper punch, and the upper punch is directly fixed on the upper punch slide; the female mold is fixed in the negative template, and both active floating suppression and forced floating suppression are performed in the pressing process. Arbitrarily selected, "powdering", floating suppression, pressure holding delay, pressure relief delay, etc. can be realized when pressing. When moving the powder, the upper and lower floating negative molds are floated synchronously with the upper punch.
3) The demoulding method has general demoulding and protection demoulding for selection; the female mold and the undershoot have simultaneous demoulding and the female mold is pulled down to directly release the mold, and the active mold release of the female mold is beneficial to better protect the product from being easily damaged.
4) Feeding height, product pressing height and demoulding position use displacement sensor to detect position and PLC program control accuracy, and with mechanical device limit.
5) A composite non-metallic material is installed at the joint between the floating plate and the cavity block of the mold frame, and the composite non-metallic material is isolated in the feeding shoe and the storage hopper, and all the metal parts are not in contact with the raw material powder.
Feeding System
1.The feeding system will have 6 hoppers, and each hopper will load different raw material.
2.The hopper can be rotated, and has good sealing.
3.Automatic loading of raw materials ,every 5-10 strokes.
4.Hopper working quantity can be set on the HMI, 1,2,3 …10 ,working together.
5.6 big hoppers will be installed on the top of machine, each hopper can load 15 Kg of powder.
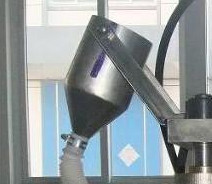
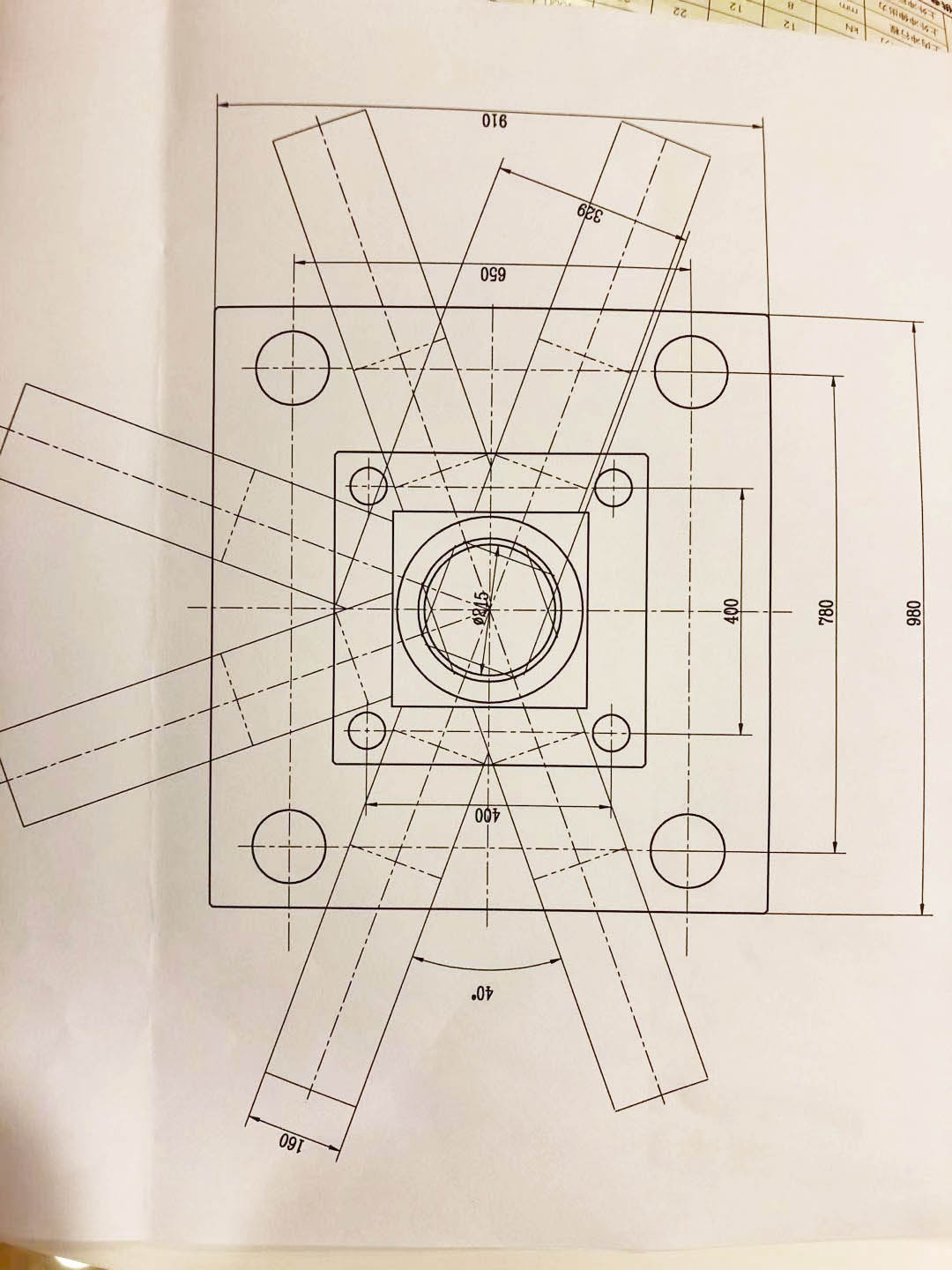
Pillar
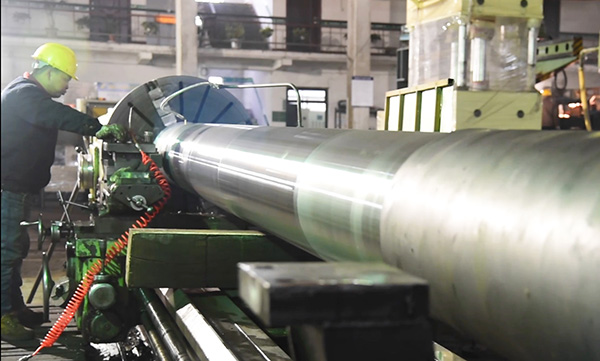
The guide columns (pillars) will be made of C45 hot forging steel and have a hard chrome coating thickness 0.08mm. And do hardening and tempering treatment.
Manufacturing Standards
JB/T3818-99《Technical conditions of hydraulic press》
GB5226.1-2002 《Safety of machinery-Mechanical and electrical equipment-Part 1: General technical requirements》
GB/T 3766-2001 《General technical requirements for hydraulic systems》
GB17120-97 《Press machinery safety technical requirements》
JB9967-99 《Hydraulic machine noise limit》
Main Body
The design of the whole machine adopts computer optimization design and analyzes with finite element. The strength and rigidity of the equipment are good, and the appearance is good. All welded parts of the machine body are welded by high-quality steel mill Q345B steel plate, which is welded with carbon dioxide to ensure the welding quality.
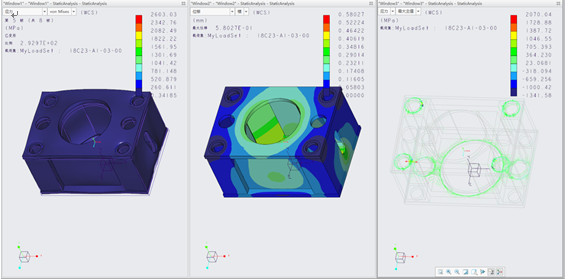
Cylinder
Parts |
Feature |
Cylinder Barrel |
|
Piston Rod |
|
Seals |
Adopt Japanese NOK brand quality sealing ring |
Piston |
Guided by copper plating, good wear resistance, ensuring long-term operation of the cylinder |
Servo System
1.Servo System Composition
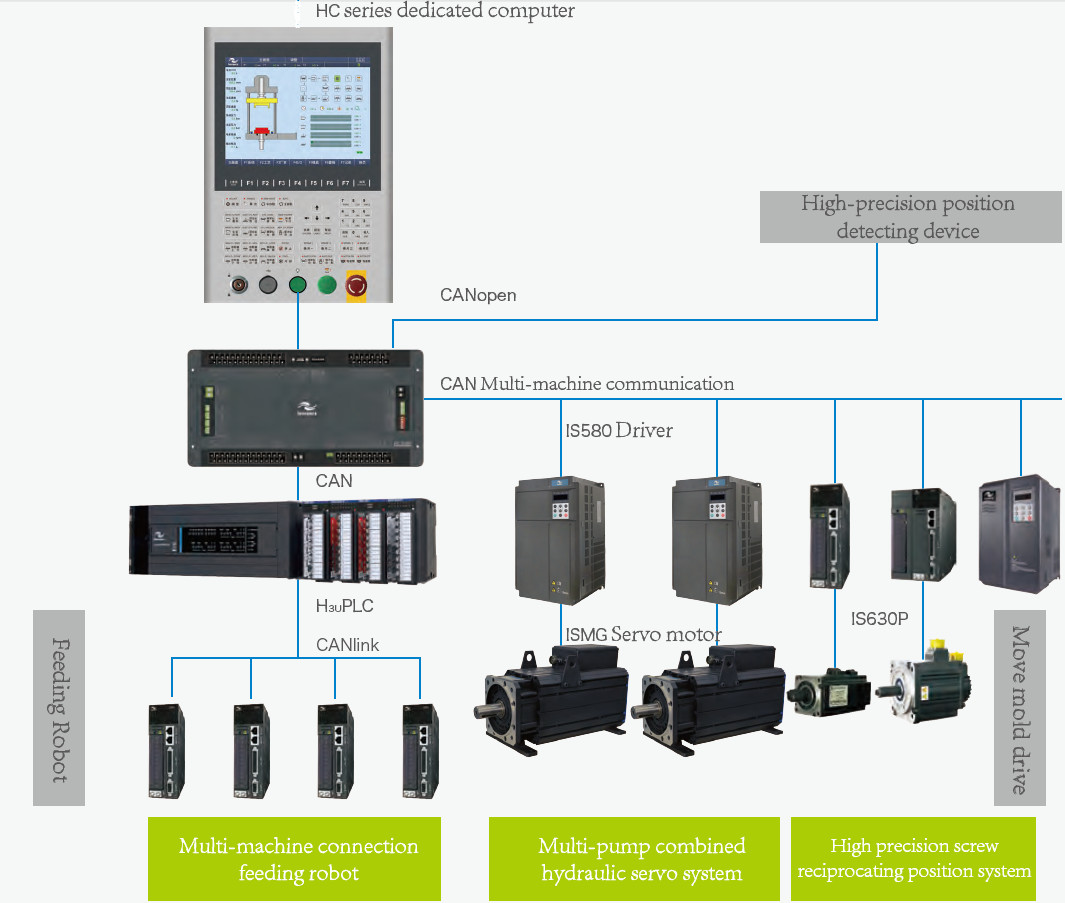
2.Advantages of Servo System
Energy saving
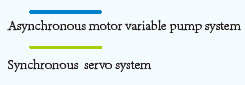
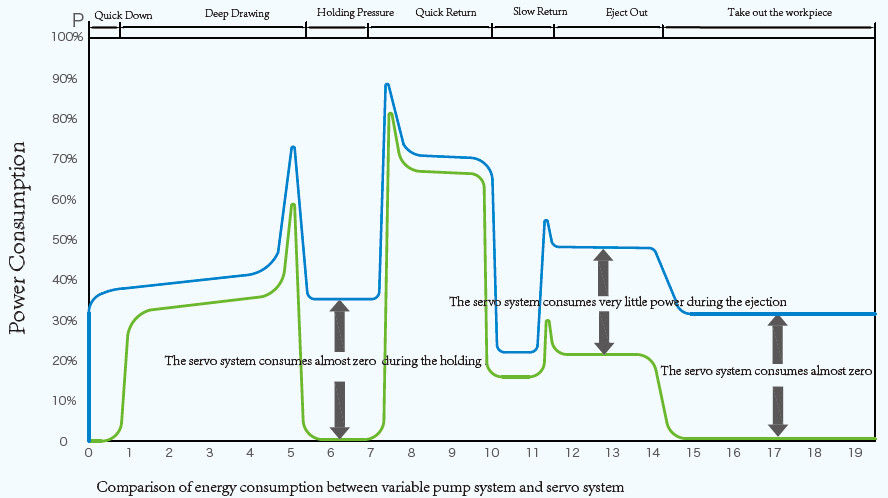
Compared with the traditional variable pump system, the servo oil pump system combines the fast stepless speed regulation characteristics of the servo motor and the self-regulating oil pressure characteristics of the hydraulic oil pump, which brings huge energy saving potential, and the energy saving rate can reach up to 30%-80%.
Efficient
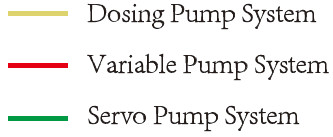
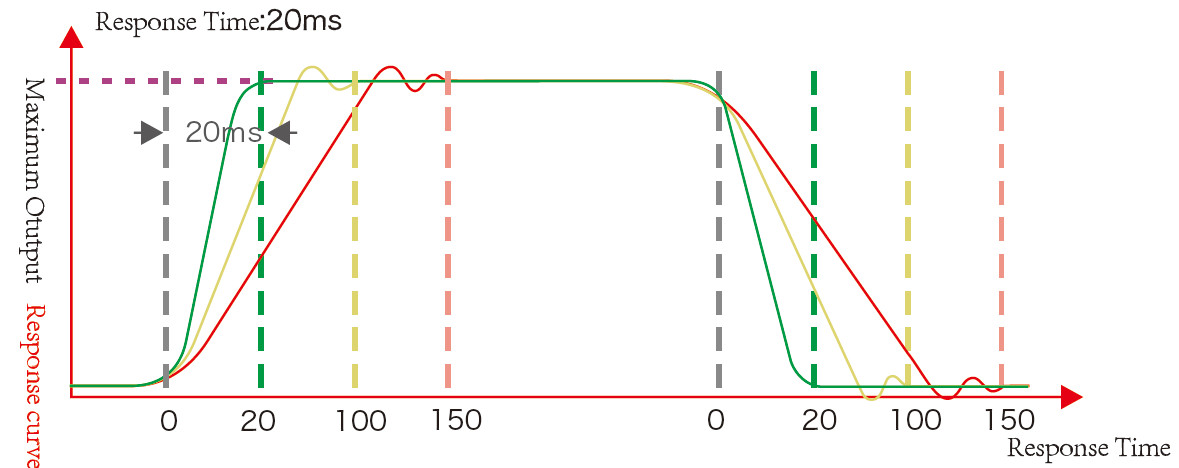
The response speed is fast and the response time is as short as 20ms, which improves the response speed of the hydraulic system.
Precision
The fast response speed guarantees the opening and closing accuracy, the position accuracy can reach 0.1mm, and the special function position positioning accuracy can reach ±0.01mm.
The high-precision, high-response PID algorithm module ensures stable system pressure and pressure fluctuations of less than ±0.5 bar, improving product quality.
Environmental protection
Noise: The average noise of the hydraulic servo system is 15-20 dB lower than that of the original variable pump.
Temperature: After the servo system is used, the hydraulic oil temperature is reduced overall, which enhances the life of the hydraulic seal or reduces the power of the cooler.
Safety Device
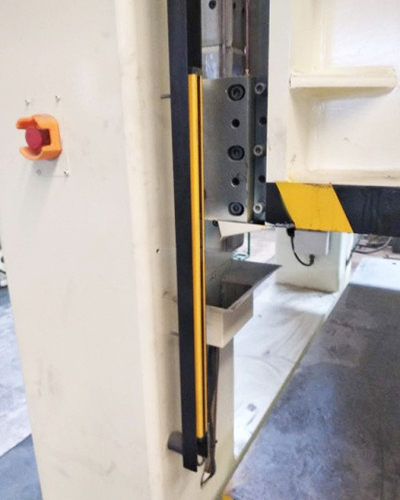
Photo-Electrical Safety Guard Front & Rear
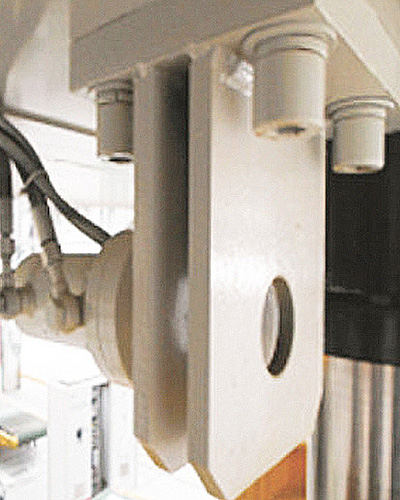
Slide Locking at TDC
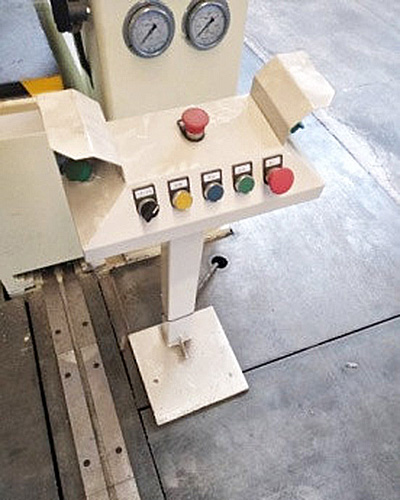
Two Hand Operation Stand
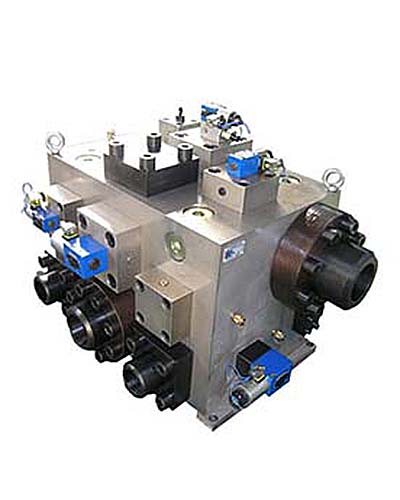
Hydraulic Support Insurance Circuit
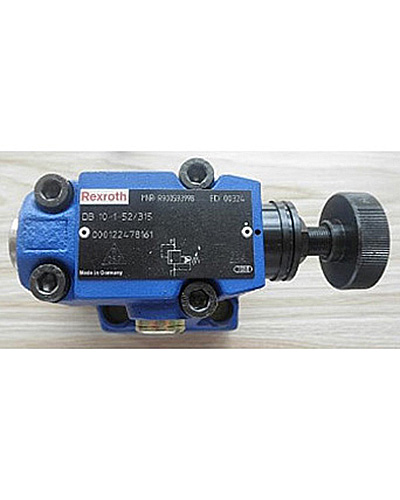
Overload Protection: Safety Valve
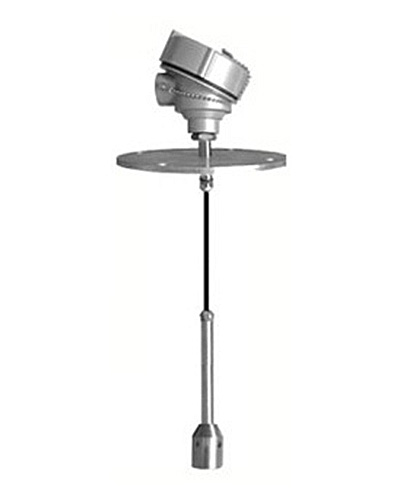
Liquid Level Alarm: Oil level
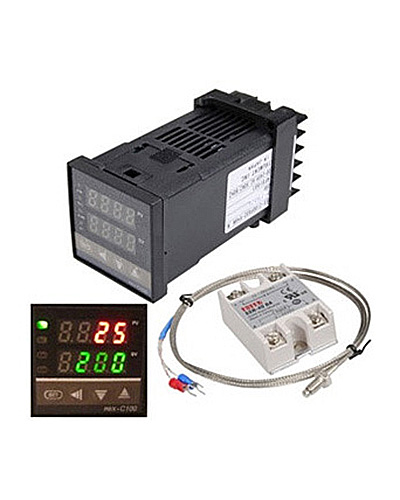
Oil temperature Warning
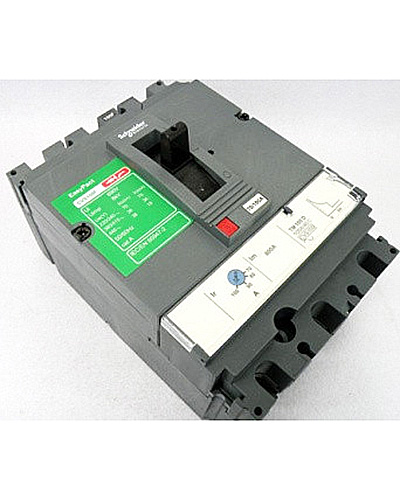
Each electrical part have overload protection
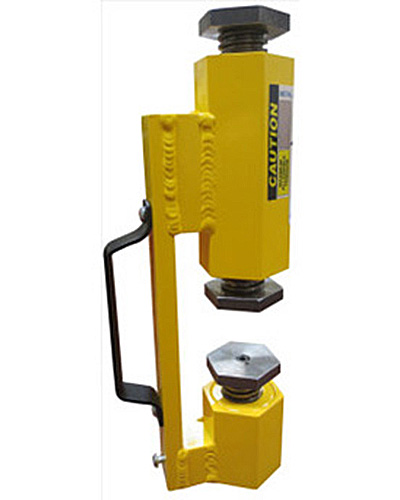
Safety blocks

Lock nuts are provided for movable parts
All action of press have safety interlock function, e.g. movable worktable will not work unless cushion return to initial position. Slide can not press when movable worktable is pressing. When conflict operation happen, alarm shows on touch screen and show what's the conflict.
Hydraulic System
1.Oil tank been set forced cooling filtering system(industrial plate-type water cooling device, cooling by circulating water, oil temperature≤55℃,make sure machine can steadily pressing in 24 hours.)
2.The hydraulic system adopts integrated cartridge valve control system with fast response speed and high transmission efficiency.
3.The oil tank is equipped with an air filter to communicate with the outside to ensure that the hydraulic oil is not polluted.
4.The connection between the filling valve and the fuel tank uses a flexible joint to prevent vibration from being transmitted to the fuel tank and completely solve the problem of oil leakage.
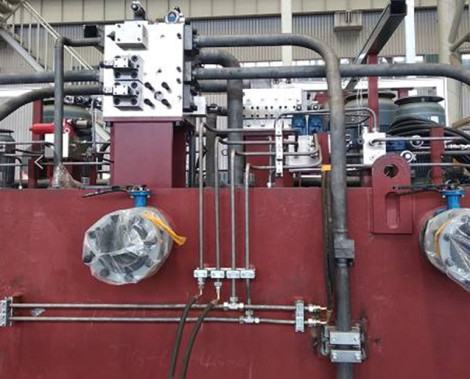