Automatic Ferrite Magnetic Hydraulic Press
Components of the machine: press (including magnetized wire package), hydraulic pump station, electric control cabinet, injection and mixing system, vacuum tank; mold frame, automatic blank taking off machine.
Whatsapp: +86 176 0282 8986
Basic Technical Specifications
1) The gear pump servo hydraulic system is used to cool the pressure oil to ensure the pressure, stability and reliability when the press is used continuously for a long time;
2) Low energy consumption and power saving. The power consumption of the whole machine is similar to that of the 150-ton press, and the output of the shift is 53% more than that of the 150-ton press;
3) The standard mold base is fixed on the host, and the mold molded parts can be quickly disassembled and replaced when the mold is replaced, and the mold base and the mold are independent;
4) The main body is a fully cast steel (or cast iron) body, and the upper and lower worktables, mold bases, magnetized wire wrapped iron cores, etc. are all cast steel parts. High mechanical strength, compact structure, small installation area, convenient for manual or automatic blank taking;
5) The main unit is four-column structure, which adopts an upper-mounted air-cooled wire package.
6) Adopt touch screen and sensor to realize man-machine interface, debugging is convenient and fast;
7) The hydraulic components of the high-pressure pump station use Italian technical valves,
8) Satisfy low-water content slurry (34% water content) automatic injection, stable and reliable suction
Company Case
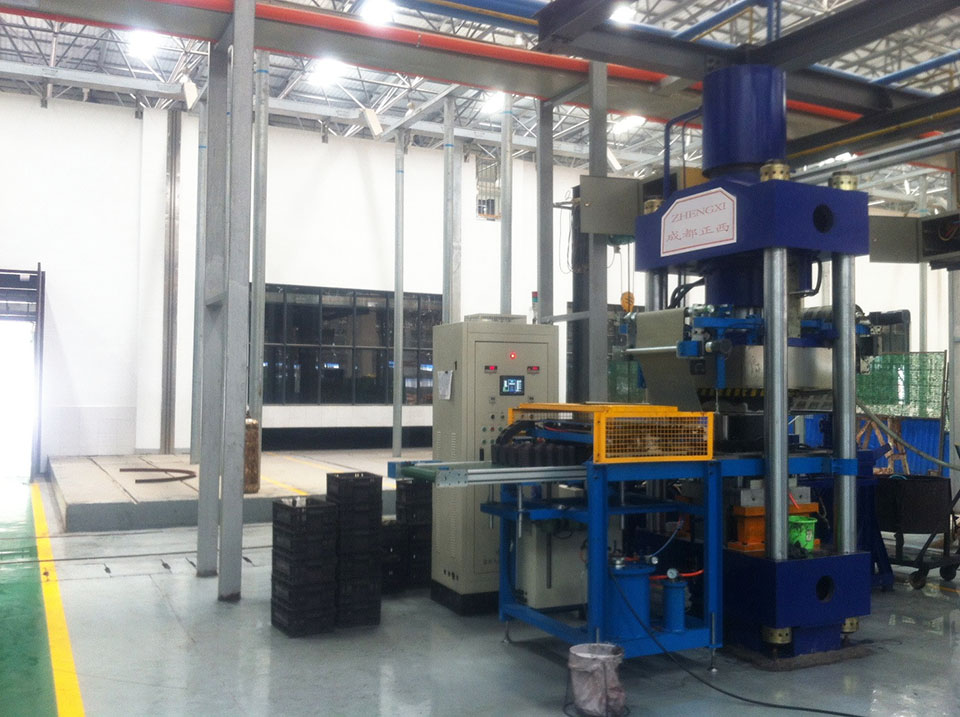
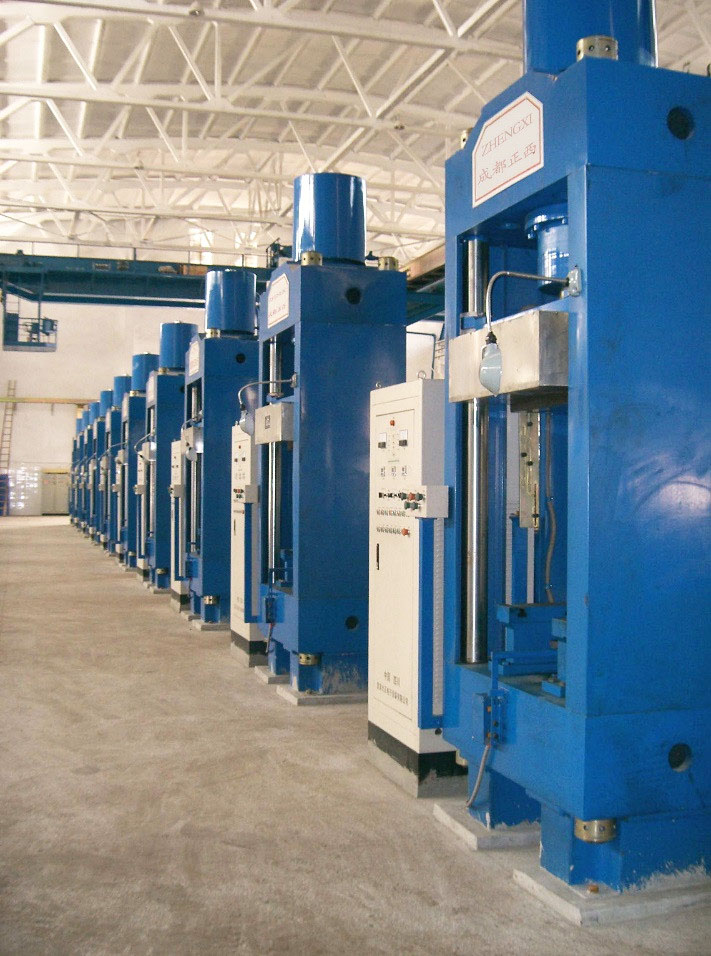

Machine Parameters
Name |
Unit |
Value |
|
Model |
/ |
YF-230T |
|
Upper cylinder force |
KN |
2300 |
|
Upper cylinder diameter |
mm |
360 |
|
Upper cylinder stroke |
mm |
495 |
|
Lower cylinder force |
KN |
1000 |
|
Lower cylinder diameter |
mm |
250 |
|
Lower cylinder stroke |
mm |
145 |
|
Ram speed |
Closing |
mm/s |
>180 |
Slow Approach |
mm/s |
2-10 |
|
Slow Pressing |
mm/s |
0.02-1.5(adjustable) |
|
Quick Pressing |
mm/s |
0.1-2.5(adjustable) |
|
Return |
mm/s |
>90 |
|
Ejection speed |
Eject out |
mm/s |
20 |
Return |
mm/s |
35 |
|
Max. free space of upper and lower worktable |
mm |
1080 |
|
Worktable size (length X width) |
mm |
1460×860 |
|
Top-mounted air-cooled wire package |
/ |
Air-cooled magnetizing coil 100000ampere-turn |
|
Max. injection volume of injection pump |
L |
4.1 |
|
Max. loading of mixer |
L |
180 |
|
Total power of the whole machine |
KW |
65 |
|
Mold base |
/ |
550mm gap between mold bases, height 300mm |
|
Cycle time |
S |
<60 |
Pillar
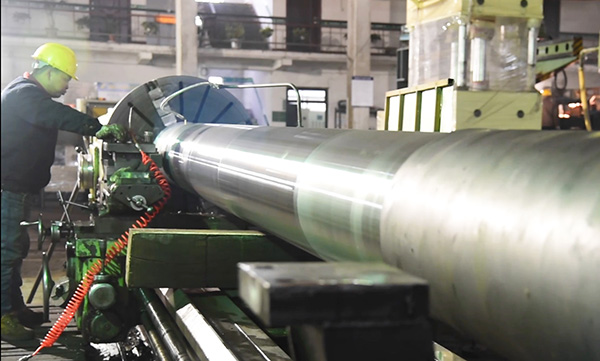
The guide columns (pillars) will be made of C45 hot forging steel and have a hard chrome coating thickness 0.08mm. And do hardening and tempering treatment.
Main Body
The design of the whole machine adopts computer optimization design and analyzes with finite element. The strength and rigidity of the equipment are good, and the appearance is good. All welded parts of the machine body are welded by high-quality steel mill Q345B steel plate, which is welded with carbon dioxide to ensure the welding quality.
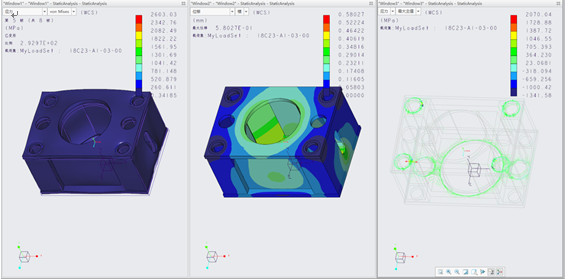
Cylinder
Parts |
Feature |
Cylinder Barrel |
|
Piston Rod |
|
Seals |
Adopt Japanese NOK brand quality sealing ring |
Piston |
Guided by copper plating, good wear resistance, ensuring long-term operation of the cylinder |
Servo System
1.Servo System Composition
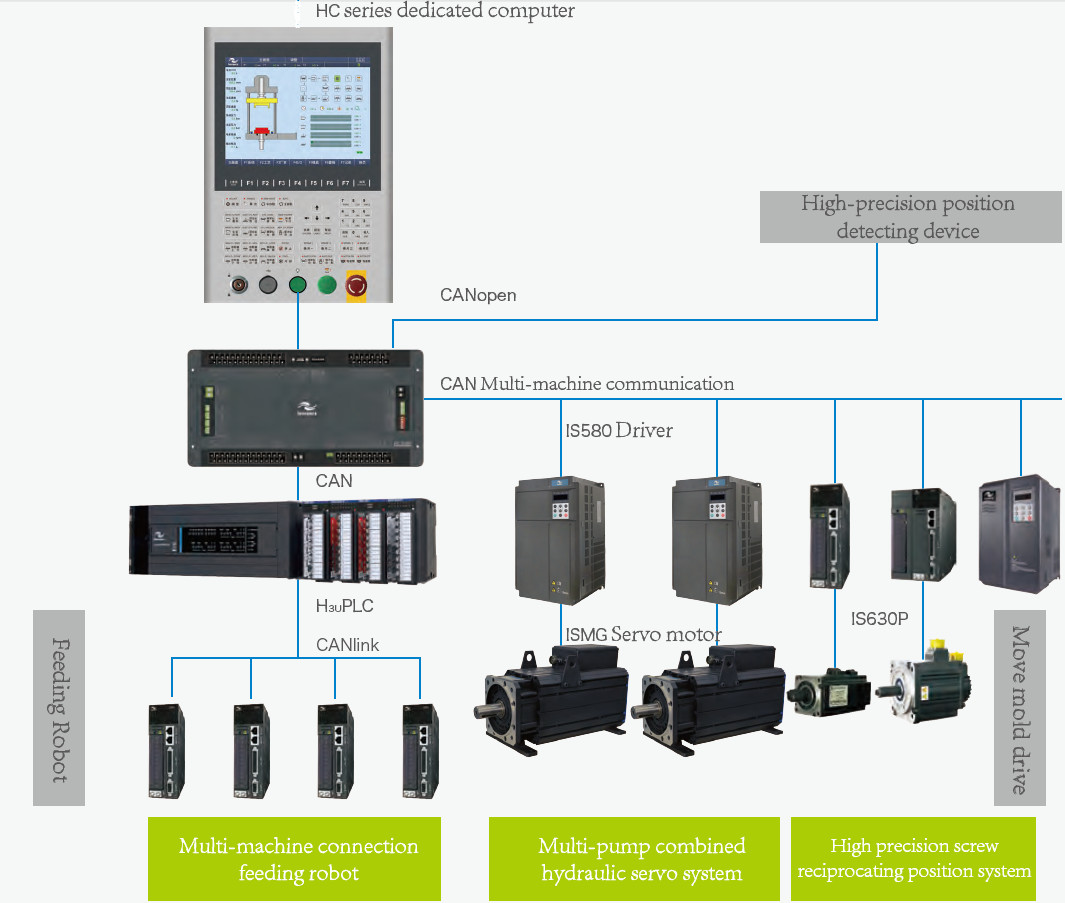
Principle of Servo Control
The main cylinder upper chamber equipped with pressure sensor, slide equipped with displacement sensor controller. According to the pressure feedback signal, the position feedback signal, pressure given signal, position given signal and speed given signal to calculate the rotational speed of the servo motor, to control the pump output for pressure, speed and position control.
The press adopts PID to adjust the pressure and position, through the speed of the servo motor to precede the closed-loop control. By adjusting the speed of the servo motor, it can control the pressure, speed, position and other parameters of the hydraulic press, by eliminating the pressure control valve, flow control valve and other components in the hydraulic control circuit to be simplify.
3.Advantages of Servo System
Energy saving
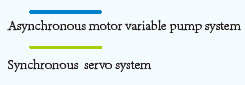
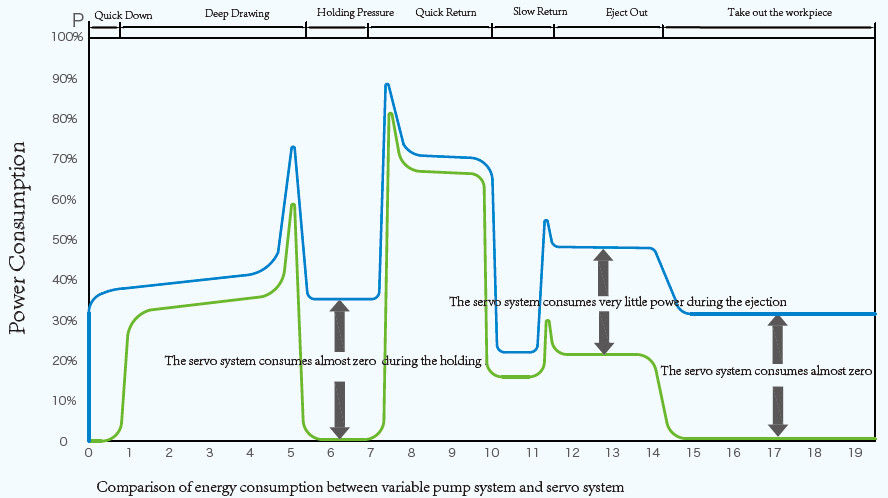
Compared with the traditional variable pump system, the servo oil pump system combines the fast stepless speed regulation characteristics of the servo motor and the self-regulating oil pressure characteristics of the hydraulic oil pump, which brings huge energy saving potential, and the energy saving rate can reach up to 30%-80%.
Efficient
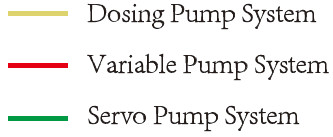
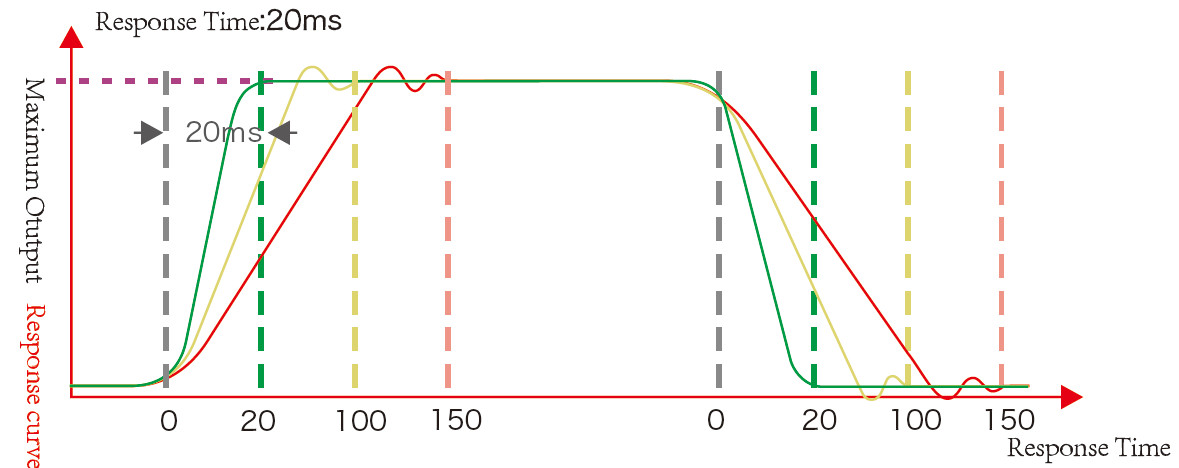
The response speed is fast and the response time is as short as 20ms, which improves the response speed of the hydraulic system.
Precision
The fast response speed guarantees the opening and closing accuracy, the position accuracy can reach 0.1mm, and the special function position positioning accuracy can reach ±0.01mm.
The high-precision, high-response PID algorithm module ensures stable system pressure and pressure fluctuations of less than ±0.5 bar, improving product quality.
Environmental protection
Noise: The average noise of the hydraulic servo system is 15-20 dB lower than that of the original variable pump.
Temperature: After the servo system is used, the hydraulic oil temperature is reduced overall, which enhances the life of the hydraulic seal or reduces the power of the cooler.
Program
Multi-screen industrial host computer realizes the main process parameters and fault prompts of the press, mainly including the following basic information:
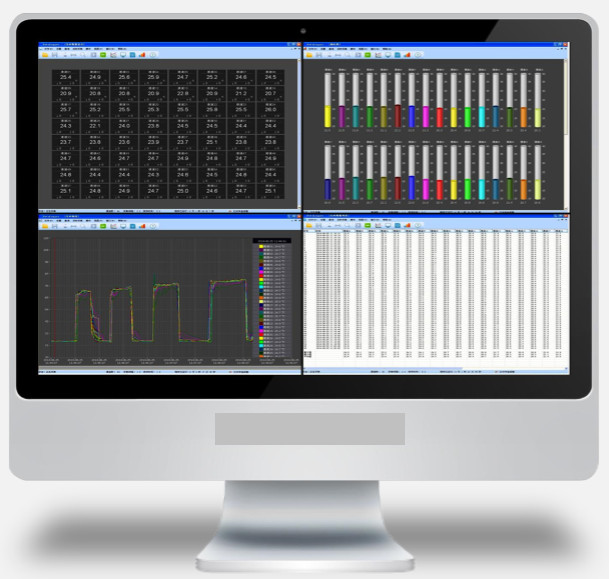
●Curve(Mpa、℃)● Password protected ●Digital display ●Data traceability
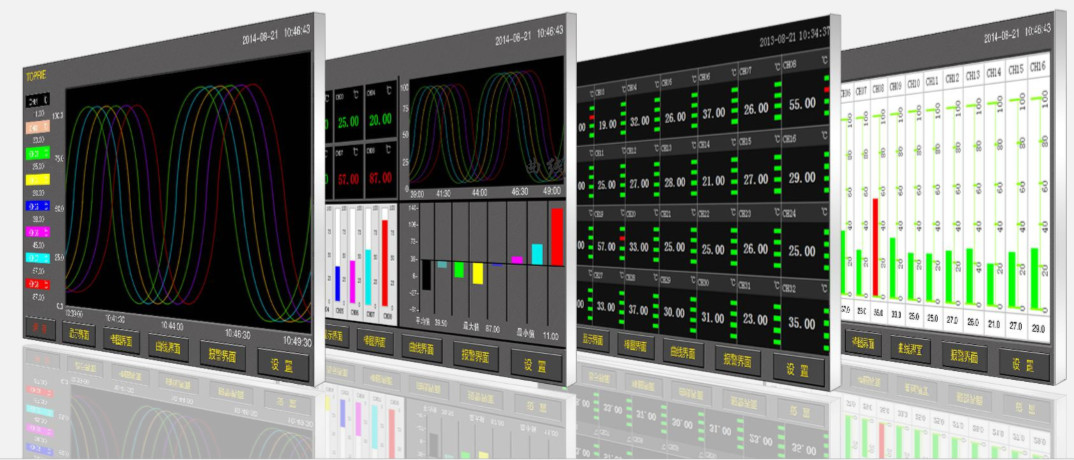
Platen position, 0 at fully open positionCycle timer
Air exhaust |
Cure cycle, stage in the program.Clamp pressure
Speed
|
Safety Device
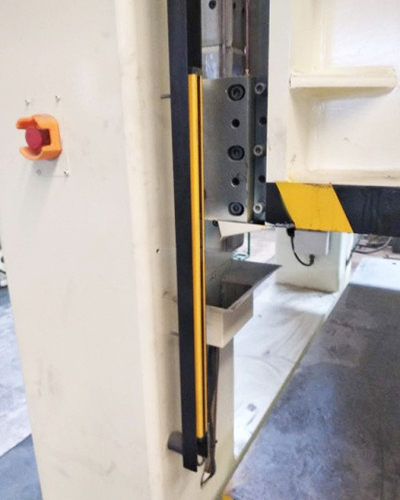
Photo-Electrical Safety Guard Front & Rear
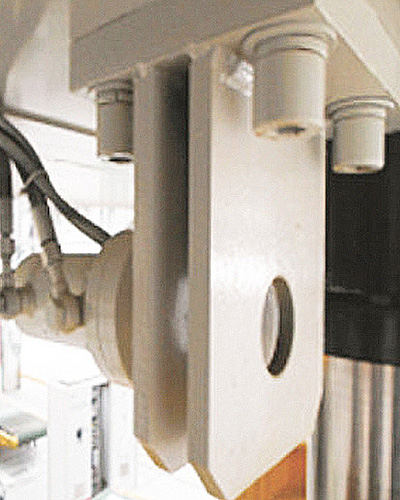
Slide Locking at TDC
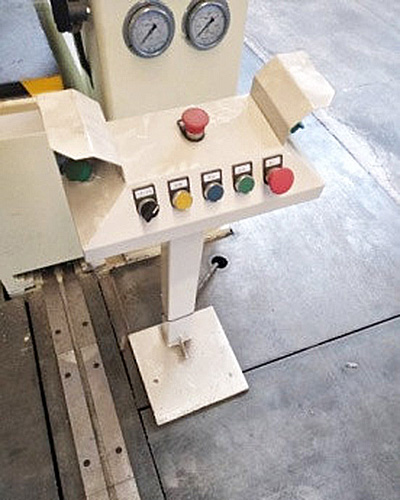
Two Hand Operation Stand
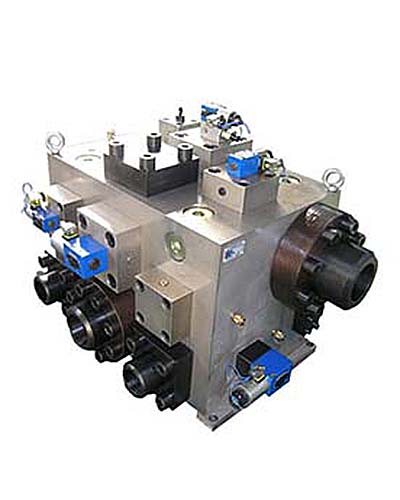
Hydraulic Support Insurance Circuit
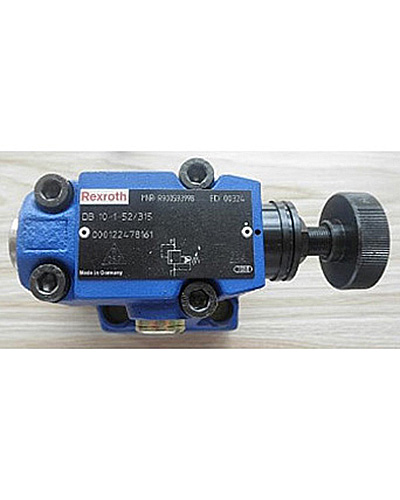
Overload Protection: Safety Valve
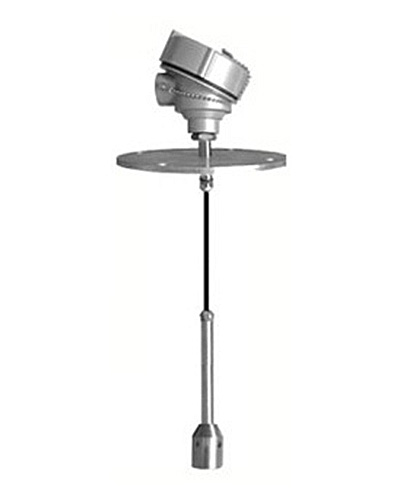
Liquid Level Alarm: Oil level
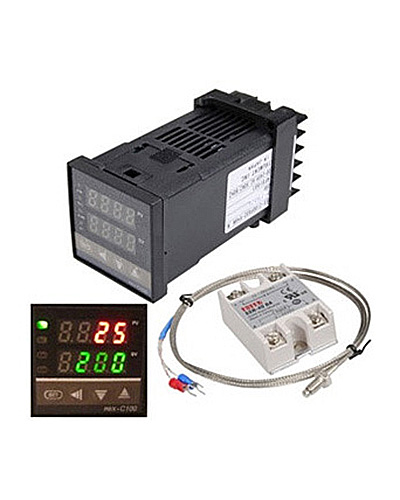
Oil temperature Warning
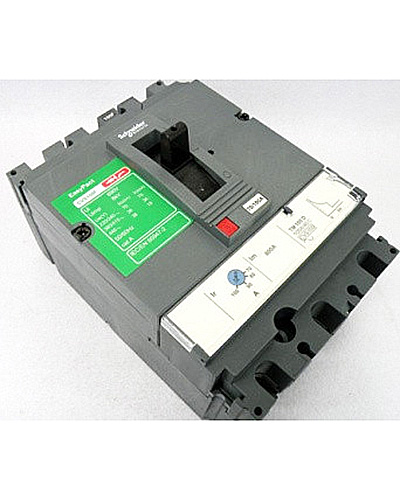
Each electrical part have overload protection
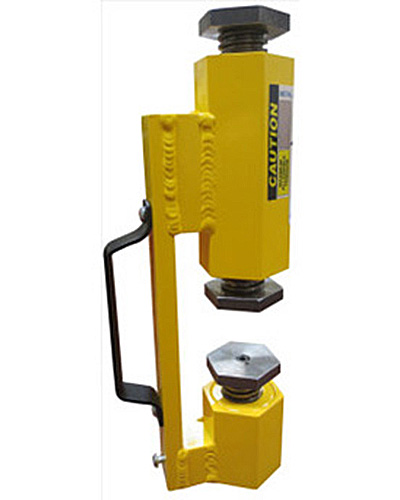
Safety blocks

Lock nuts are provided for movable parts
All action of press have safety interlock function, e.g. movable worktable will not work unless cushion return to initial position. Slide can not press when movable worktable is pressing. When conflict operation happen, alarm shows on touch screen and show what's the conflict.
Hydraulic System
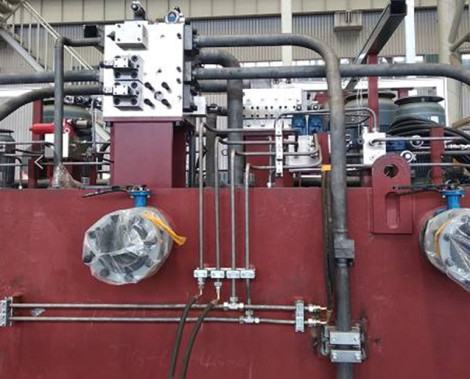
Feature
1.Oil tank been set forced cooling filtering system(cooling by oil chiller, oil temperature≤55℃,make sure machine can steadily pressing in 24 hours.)
2.The hydraulic system adopts integrated cartridge valve control system with fast response speed and high transmission efficiency.
3.The oil tank is equipped with an air filter to communicate with the outside to ensure that the hydraulic oil is not polluted.
4.The connection between the filling valve and the fuel tank uses a flexible joint to prevent vibration from being transmitted to the fuel tank and completely solve the problem of oil leakage.
5.The hydraulic oil pipe is mainly made of seamless steel pipe, and the large diameter oil path is flanged. The pipe connection is connected by SAE flange as much as possible. It is a butt welding type with good welding effect and effectively solves the oil leakage problem caused by poor welding.